Service Overview
On-premise refers to installing and running software directly on a company’s own server.
Miracom's MES implementation service caters to each customer's manufacturing environment, from consulting to solution provision, system construction, and operation.
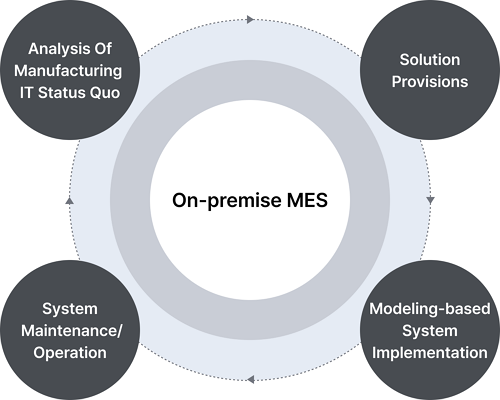
On-Premise MES Manufacturing IT Status Analysis Solution Provision System Maintenance/Operation Modeling-based System Establishment
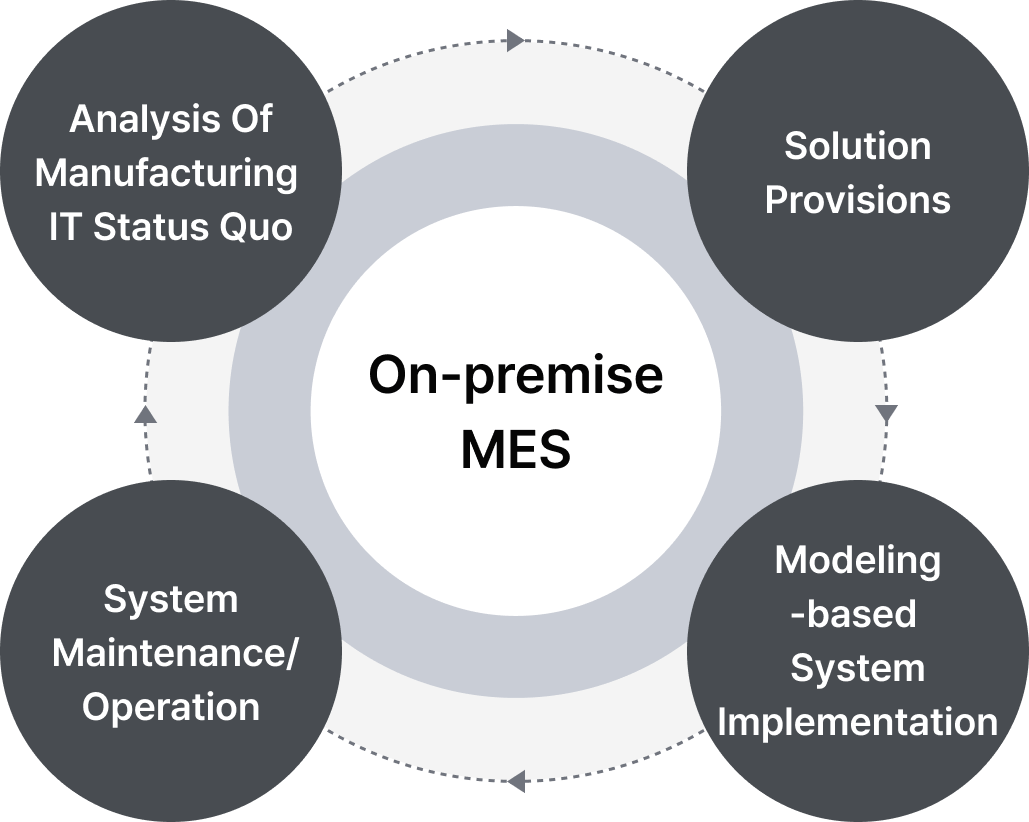
On-Premise MES Manufacturing IT Status Analysis Solution Provision System Maintenance/Operation Modeling-based System Establishment
-
- 1
Analysis of Manufacturing IT Status Quo
- Analysis of systems and data, legacy interfaces, and process status at the production site
-
- 2
Solution Provisions
- Provision of solutions including MES, QMS/EES, dashboard, and KPI reporting solutions to optimize manufacturing execution
-
- 3
Modeling-based System Implementation
- Standard process-based modeling and Customized system building for customers
-
- 4
System Maintenance/
Operation- Continuous system management, prompt technical support and performance optimization