Service Overview
To realize a smart factory, it is necessary to collect data from machines in real time and control machines according to the occurrence of events.
Miracom converts customer's manufacturing site into an automated environment where data flows by retrofitting machines and connecting machines via machine interfaces.
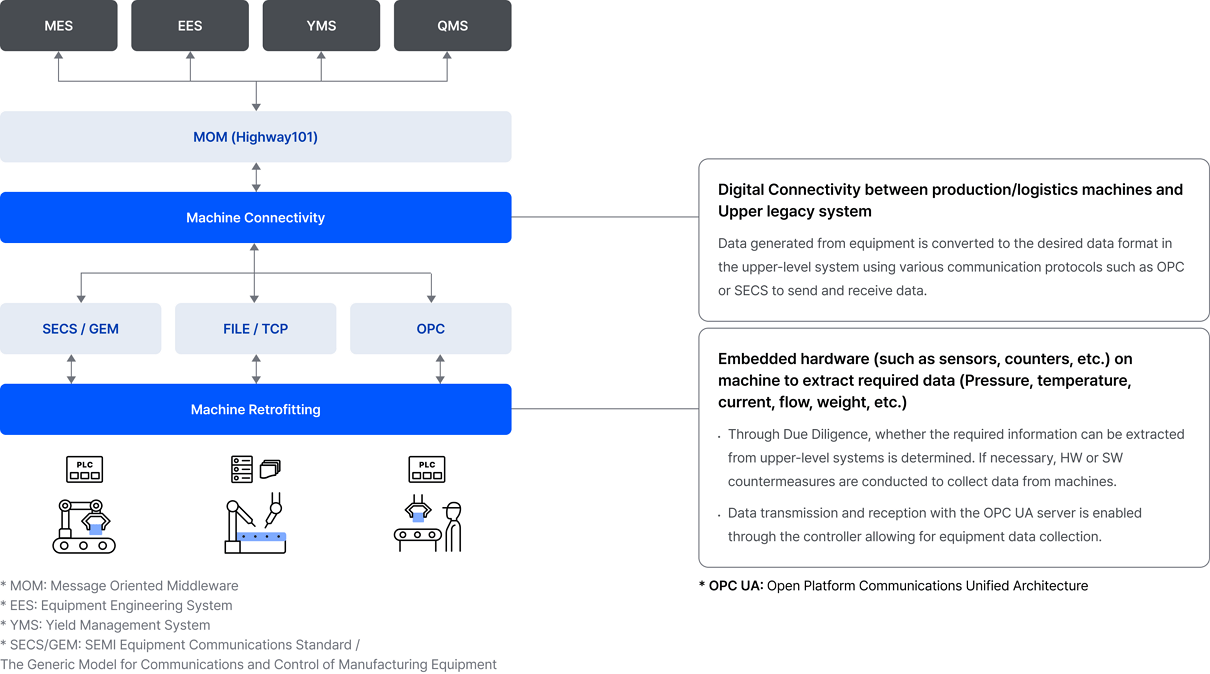
- MOM(Highway101)
- MES
- EES
- YMS
- QMS
- I/F (MC)
- SECS/GEM
- FILE/TCP
- OPC
- Machine Retrofitting
- Digital Connectivity between production/logistics machines and Upper legacy system
- Data generated from equipment is converted to the desired data format in the upper-level system using various communication protocols such as OPC or SECS to send and receive data.
- Embedded hardware (such as sensors, counters, etc.) on machine to extract required data (Pressure, temperature, current, flow, weight, etc.)
- Through Due Diligence, whether the required information can be extracted from upper-level systems is determined. If necessary, HW or SW countermeasures are conducted to collect data from machines.
- Data transmission and reception with the OPC UA server is enabled through the controller allowing for equipment data collection.
- *OPC UA : Open Platform Communications Unified Architecture
- * MOM : Message Oriented Middleware
- * EES : Equipment Engineering System
- * YMS : Yield Management System
- * SECS/GEM : SEMI Equipment Communications Standard / The Generic Model for Communications and Control of Manufacturing Equipment
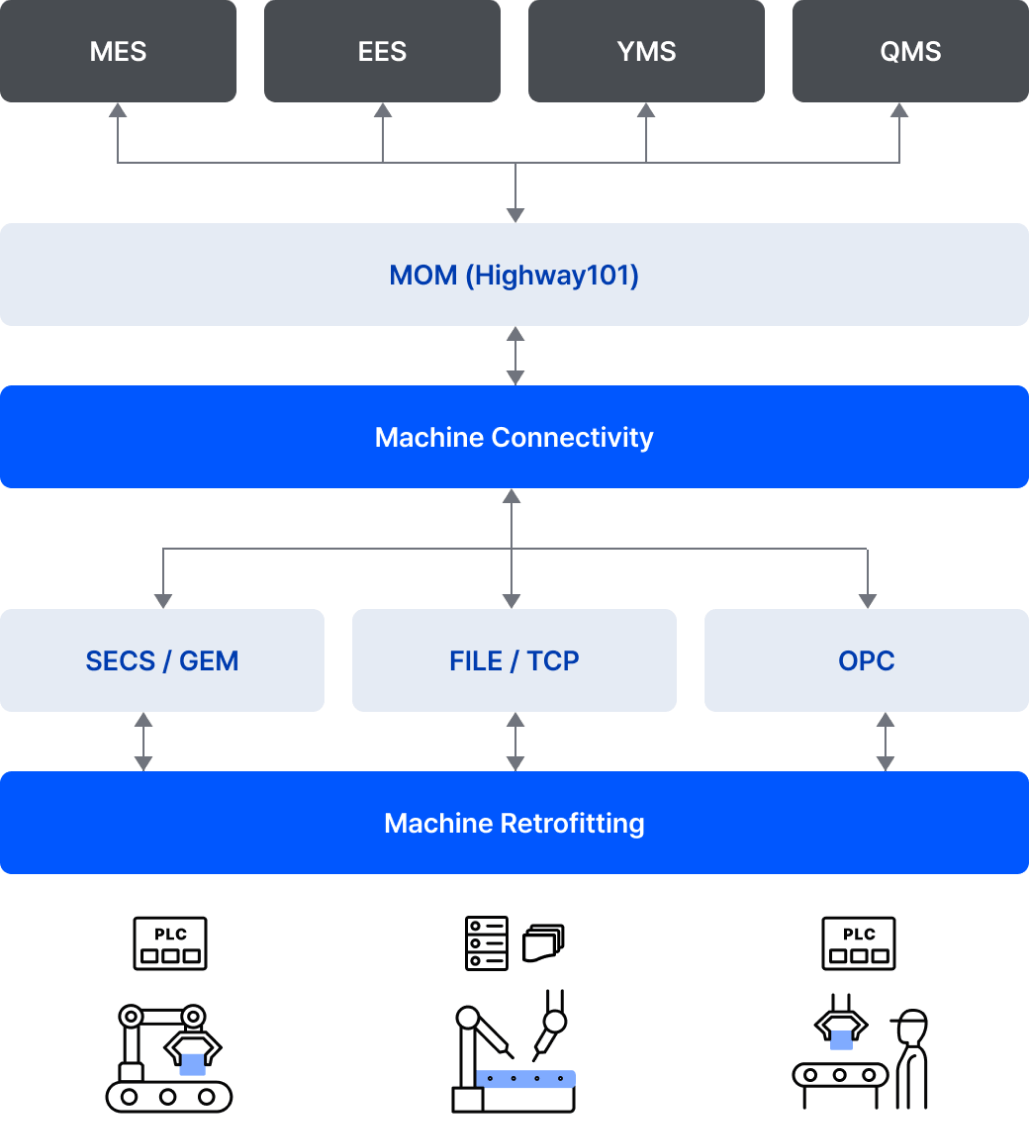
- MOM(Highway101)
- MES
- EES
- YMS
- QMS
- I/F (MC)
- SECS/GEM
- FILE/TCP
- OPC
- Machine Retrofitting
-
- Digital Connectivity between production/logistics machines and Upper legacy system
- Data generated from equipment is converted to the desired data format in the upper-level system using various communication protocols such as OPC or SECS to send and receive data.
-
- Embedded hardware (such as sensors, counters, etc.) on machine to extract required data (Pressure, temperature, current, flow, weight, etc.)
- Through Due Diligence, whether the required information can be extracted from upper-level systems is determined. If necessary, HW or SW countermeasures are conducted to collect data from machines.
- Data transmission and reception with the OPC UA server is enabled through the controller allowing for equipment data collection.
* OPC UA: Open Platform Communications Unified Architecture
* EES: Equipment Engineering System
* YMS: Yield Management System
* SECS/GEM: SEMI Equipment Communications Standard / The Generic Model for Communications and Control of Manufacturing Equipment
"Cloud-based machine connectivity through Edge Device" helps clients easily collect, connect, and utilize machine data in the cloud environment.
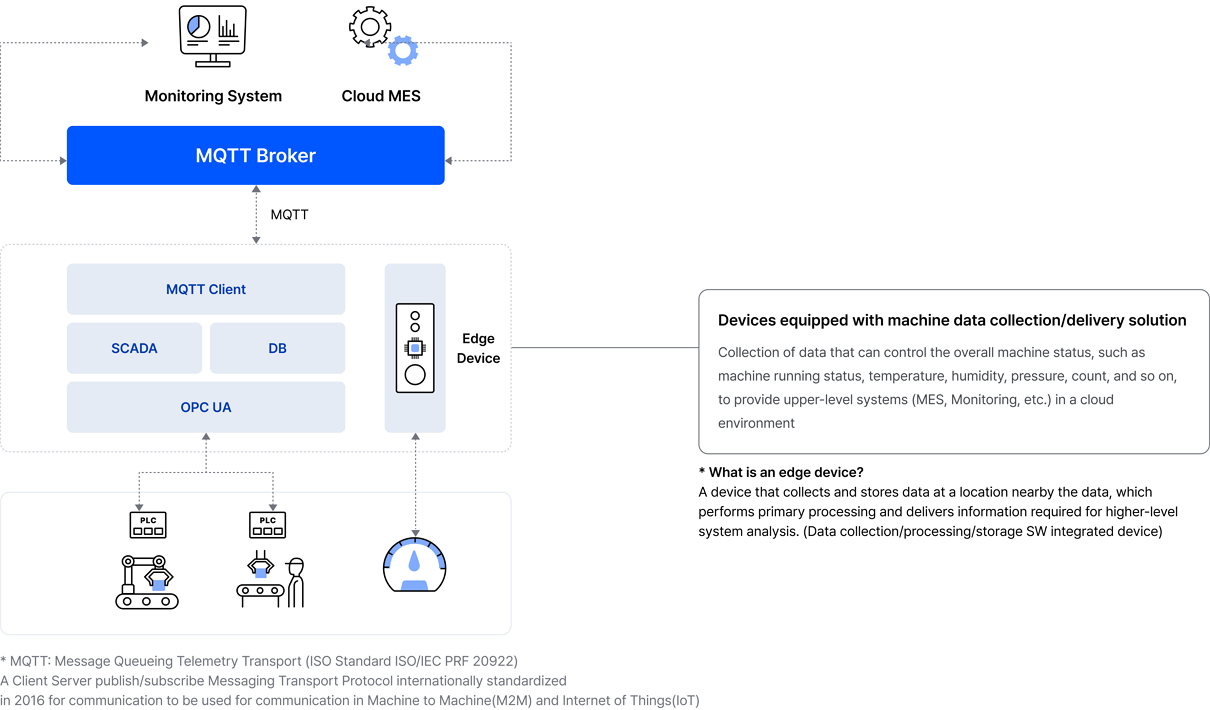
- MQTT Broker
- Monitoring System
- Cloud MES
- Edge Device
- MQTT Client
- SCADA
- DB
- OPC UA
- Devices equipped with machine data collection/delivery solution
-
Collection of data that can control the overall machine status, such as machine running status, temperature, humidity, pressure, count, and so on, to provide upper-level systems (MES, Monitoring, etc.) in a cloud environment
* What is an edge device? A device that collects and stores data at a location nearby the data, which performs primary processing and delivers information required for higher-level system analysis. (Data collection/processing/storage SW integrated device)
- * MQTT : Message Queueing Telemetry Transport (ISO Standard ISO/IEC PRF 20922) A Client Server publish/subscribe Messaging Transport Protocol internationally standardized in 2016 for communication to be used for communication in Machine to Machine(M2M) and Internet of Things(IoT)
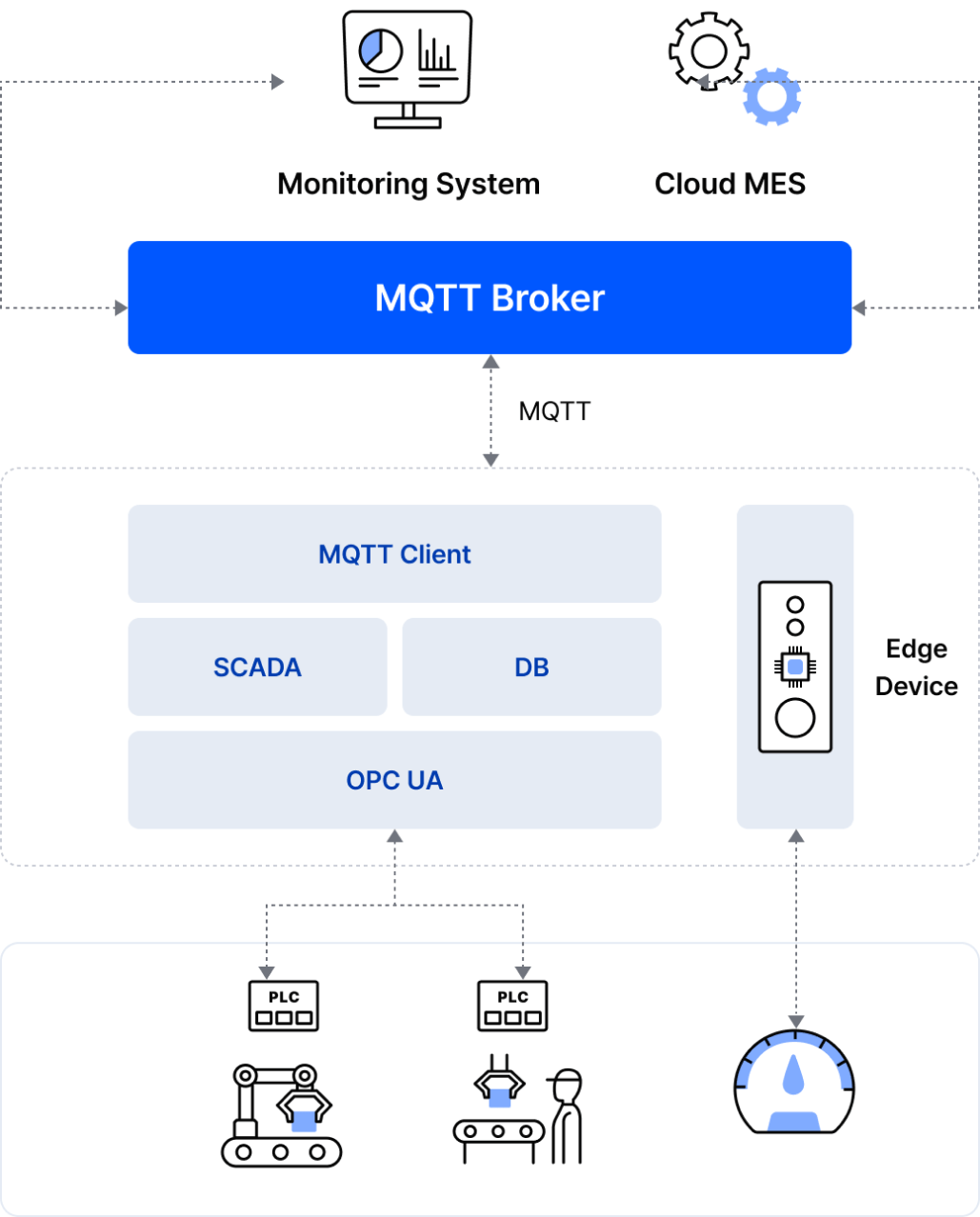
- MQTT Broker
- Monitoring System
- Cloud MES
- Edge Device
- MQTT Client
- SCADA
- DB
- OPC UA
-
- Devices equipped with machine data collection/delivery solution
-
Collection of data that can control the overall machine status, such as machine running status, temperature, humidity, pressure, count, and so on, to provide upper-level systems (MES, Monitoring, etc.) in a cloud environment
* What is an edge device?
A device that collects and stores data at a location nearby the data, which performs primary processing and delivers information required for higher-level system analysis. (Data collection/processing/storage SW integrated device)
* MQTT: Message Queueing Telemetry Transport (ISO Standard ISO/IEC PRF 20922) A Client Server publish/subscribe Messaging Transport Protocol internationally standardized in 2016 for communication to be used for communication in Machine to Machine(M2M) and Internet of Things(IoT)