Implementation of automation of conveyance tasks that move materials/semi-finished products from the current process (machine/system) to the next process by utilizing either automated or autonomous equipment such as AGV, AMR, and OHT. By applying a system akin to autonomous driving technology, it improves efficiency through optimal route navigation, or following a predetermined path, without separate on-spot guidance and realizes safe unmanned delivery.
AGV |
AMR |
OHT |
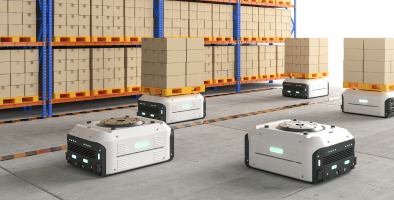 |
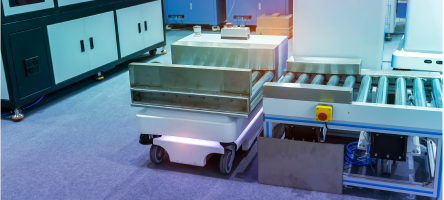 |
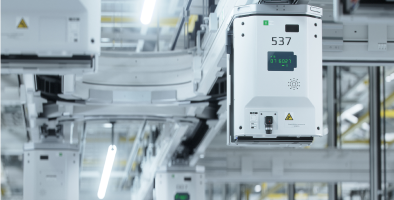 |
An unmanned transport machine that travel on predetermined routes to do repetitive tasks
|
A machine that’s not only self-driven, but can also choose optimal route using laser-based navigation and perception algorithms
|
An automated transport system that travels across overhead rails
Maximum utilization of ceiling space
|
-
AGV
An unmanned transport machine that travel on predetermined routes to do repetitive tasks
-
AMR
A machine that’s not only self-driven, but can also choose optimal route using laser-based navigation and perception algorithms
-
OHT
An automated transport system that travels across overhead rails
Maximum utilization of ceiling space
We efficiently implement storage automation in limited areas or spaces by utilizing equipment such as stacker cranes and multi-shuttle. Depending on the size of the product, it is divided into pallet or box type, and the optimal solution is selected and provided allowing for the customer's environment such as storage efficiency and processing volume.
Pallet Storage Type |
Stacker Crane |
Shuttle |
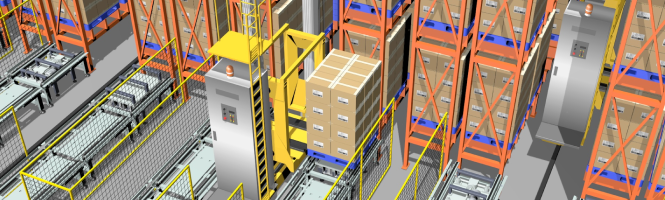 |
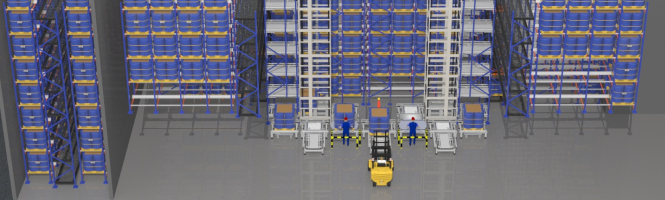 |
Handling Bulk Product (Pallet)
Automated palletizing, storage, and retrieval system with crane
High storage capacity in limited space
Crane throughput calculation considering inbound and outbound volume, storage volume, and floor height, etc.
|
Handling Bulk Product (pallets)
System that automatically receives/stores/releases pallets in racks via Shuttle
Maximum storage capacity in the same area
Type selection based on inbound and outbound volume, storage volume, movement, etc.
|
Box Storage Type |
Shuttle |
Mini-Loader |
AutoStore |
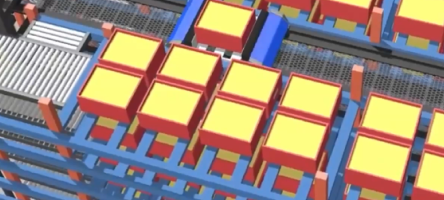 |
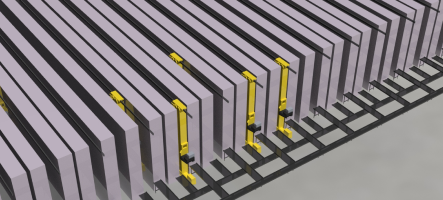 |
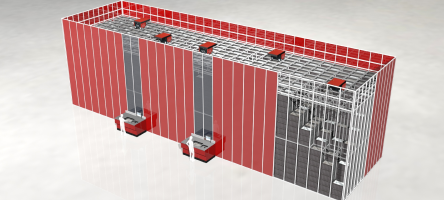 |
Handling Lightweight/Low-volume product (Bucket)
Shuttles and lifters enabling automated receiving/storage/retrieval system
|
Handling Lightweight/Low-Volume Product (Bucket)
Mini cranes enabling automated receiving/storage/shipping system
|
Handling Light/Low Volume Products (Buckets)
A system where robots automatically receiving/storage/shipping from the top of the grid
|
Pallet Storage Type
-
Stacker Crane
Handling Bulk Product (Pallet)
Automated palletizing, storage, and retrieval system with crane
High storage capacity in limited space
Crane throughput calculation considering inbound and outbound volume, storage volume, and floor height, etc.
-
Shuttle
Handling Bulk Product(pallets)
System that automatically receives/stores/releases pallets in racks via Shuttle
Maximum storage capacity in the same area
Type selection based on inbound and outbound volume, storage volume, movement, etc.
Box Storage Type
-
Shuttle
Handling Lightweight/Low-volume product (Bucket)
Shuttles and lifters enabling automated receiving/storage/retrieval systems
-
Mini-Loader
Handling Lightweight/Low-volume product (Bucket)
Mini cranes enabling automated receiving/storage/shipping system
-
AutoStore
Handling Lightweight/Low-volume product (Bucket)
A system where robots automatically receiving/storage/shipping from the top of the grid
Warehousing and shipment automation is classified into picking and sorting automation equipment, which utilize picking robots, sorters, and QPS to reduce human error and improve speed and accuracy.
Picking/Sorting Machine/System |
Robot Picking |
Sorter (Automatic) |
QPS |
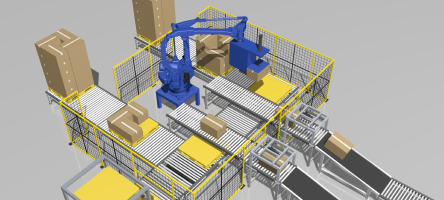 |
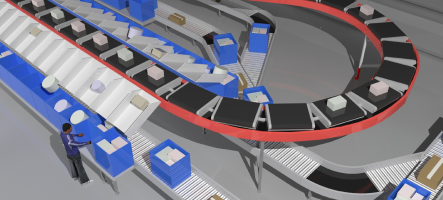 |
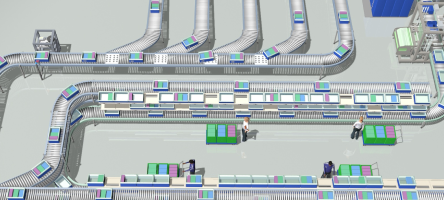 |
Automated robotic picking by identifying product characteristics
Applicable to a variety of environments, from small products to boxes
|
Equipment that quickly recognizes barcodes on products and sorts them automatically
Deployment of the suitable type of sorter based on product shape, size, weight, throughput, etc.
|
A system that automatically transports boxes with goods to stations that require picking, and workers pick or sort by checking lighted indicators.
Minimizing worker movements and streamlining work loads
|
*QPS: Quick Picking System
We provide a 3D-based logistics site real-time monitoring/control system, including facility operation status, failure notification, and operation status visualization. (MiiT : Miracom Digital Twin Platform)
The system enables integrated field management from failure detection/analysis/action to real-time status/alarm data.
Monitoring Failure Detection Failure Cognition Alarm Broadcasting System Failure-related information inquiry failure analysis Simple action Collaboration on-site action PC operator CCTV PLC/PC remote control control room Advanced technicians & field workers Collaboration control center Facility status indicators CCTV video
-
1Logistics Monitoring
Visualizing equipment uptime, failure notifications, and operational status.
-
2Collection and Analysis of Logistics Movement Data
System and Machine Interfaces
Fault Analysis/Tracking
-
3Intelligent Fault Detection/Countermeasure
AI-based automatic detection utilizing parent system/CCTV
Remote action for simple troubleshooting
Real-time collaboration with warehouse workers
-
1Logistics Monitoring
Visualizing equipment uptime, failure notifications, and operational status.
-
2Collection and Analysis of Logistics Movement Data
System and Machine Interfaces
Fault Analysis/Tracking
-
3Intelligent Fault Detection/Countermeasure
AI-based automatic detection utilizing parent system/CCTV
Remote action for simple troubleshooting
Real-time collaboration with warehouse workers