Why Needed?
IT Operations (ITOps) services are a must for organized IT operations and cost savings.
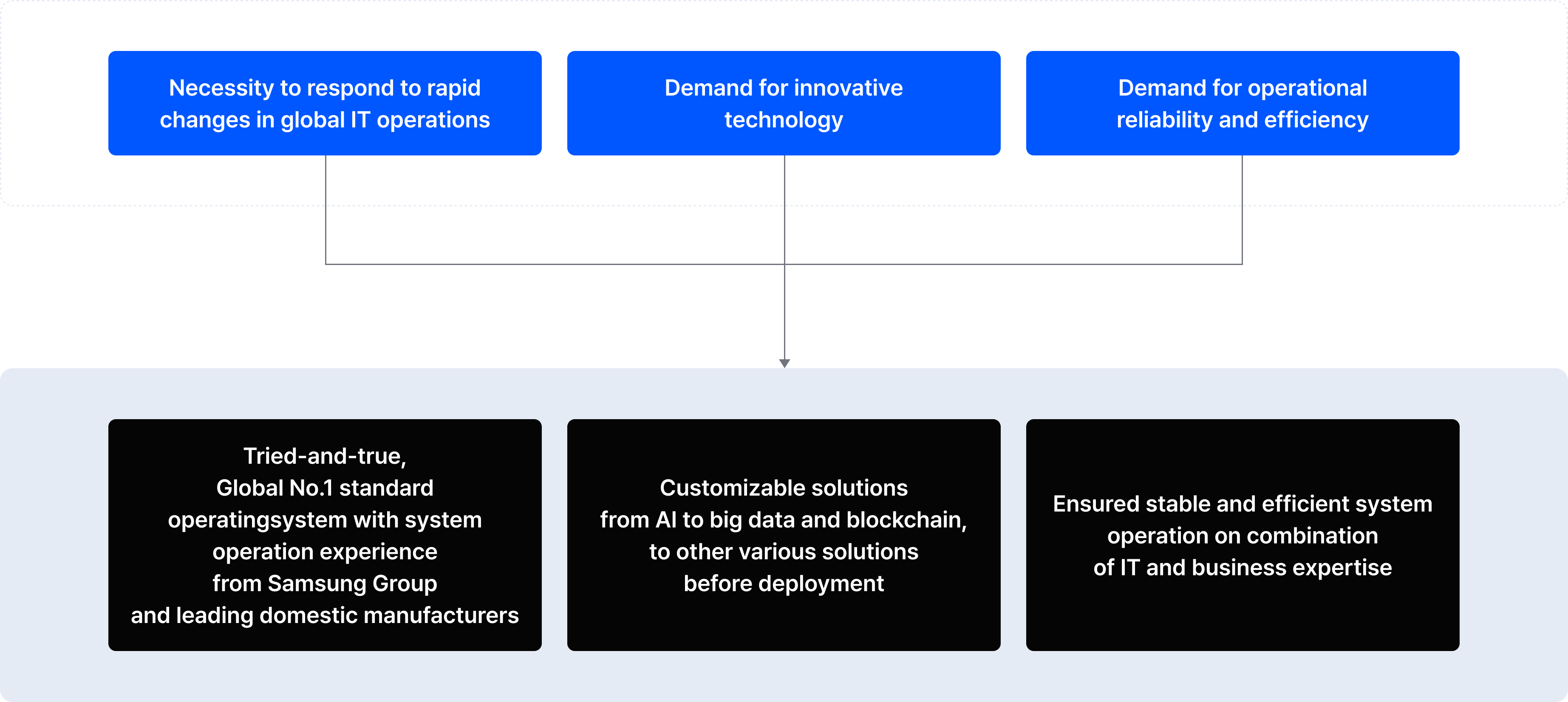
Necessity to respond to rapid changes in global IT operations, Demand for innovative technology, Demand for operational reliability and efficiency -> tried-and-true,global NO.1 standard operatingsystem with system operation experience from Samsung Group and leading domestic manufacturers, Customizable solutions from AI to big data and blockchain, to other various solutions before deployment, Ensured stable and efficient system operation on combination of IT and business expertise
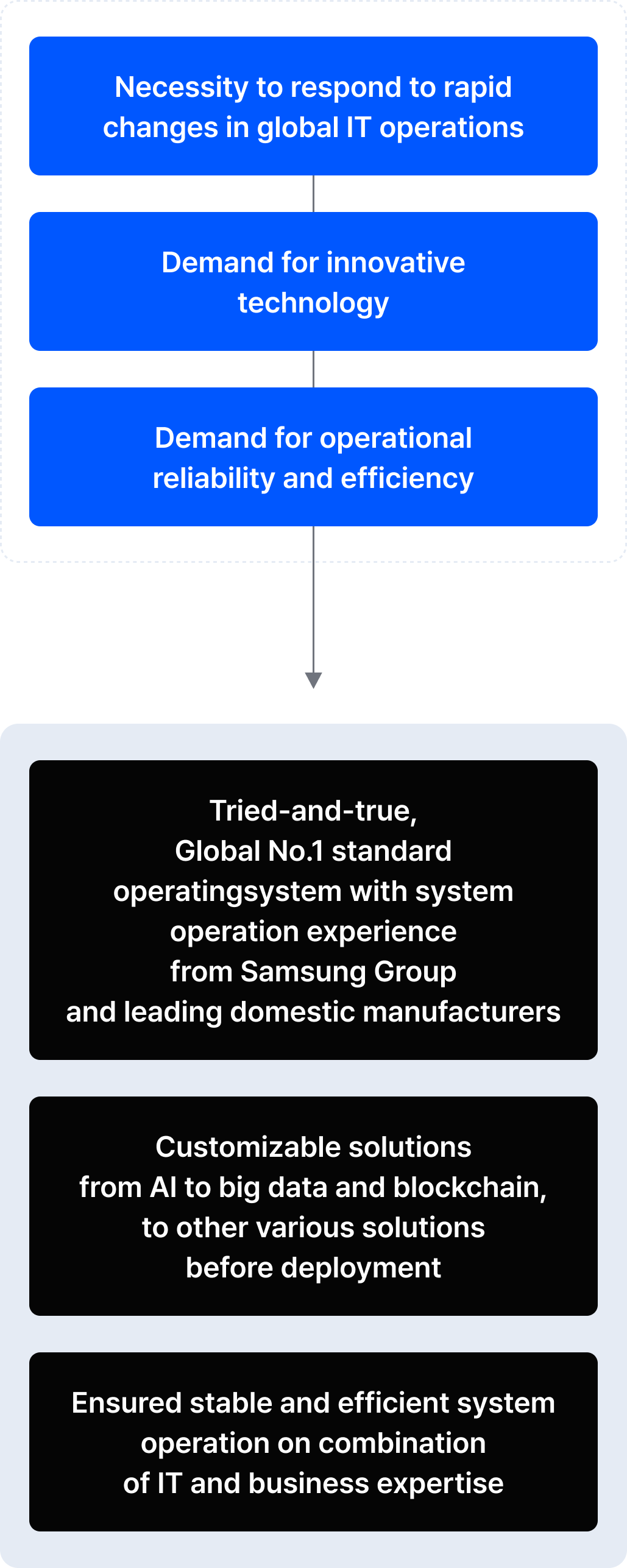
Necessity to respond to rapid changes in global IT operations, Demand for innovative technology, Demand for operational reliability and efficiency -> tried-and-true,global NO.1 standard operatingsystem with system operation experience from Samsung Group and leading domestic manufacturers, Customizable solutions from AI to big data and blockchain, to other various solutions before deployment, Ensured stable and efficient system operation on combination of IT and business expertise